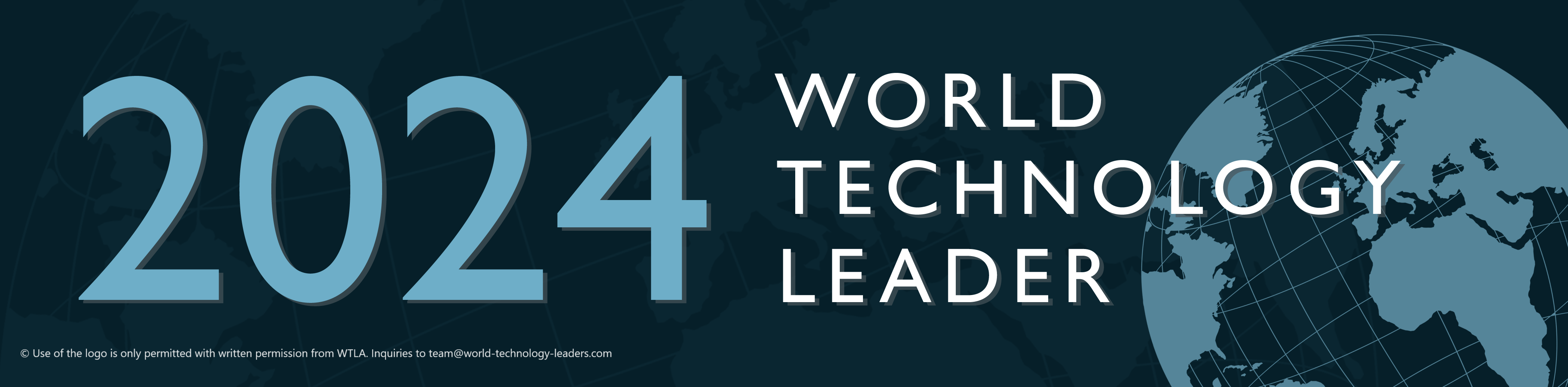
Combining Software with engineering
Awarded for
Company
Dürr is one of the world’s leading mechanical and plant engineering firms with particular expertise in the technology fields of automation, digitalization, and energy efficiency. Even though the organization has developed software solutions for over 25 years, the foundation of Dürr’s so-called “Digital Factory” in 2018 marked a major milestone in the accelerated expansion of the digital expertise. Together with Dürr’s sub-brand iTAC Software AG – a global software and IT company and a leading MES/MOM provider – the Digital Factory has established a virtual organization that focusses on the strategic development of digital solution that drive the Overall Equipment Effectiveness (OEE). Around 200 staff drive the digital transformation from a simple product idea right to the after-sales-services of the complete software lifecycle. Not only previous awards and rankings, but equally various successful customer references have proven the well-established position of the Digital Factory in the automotive and discrete production sectors.
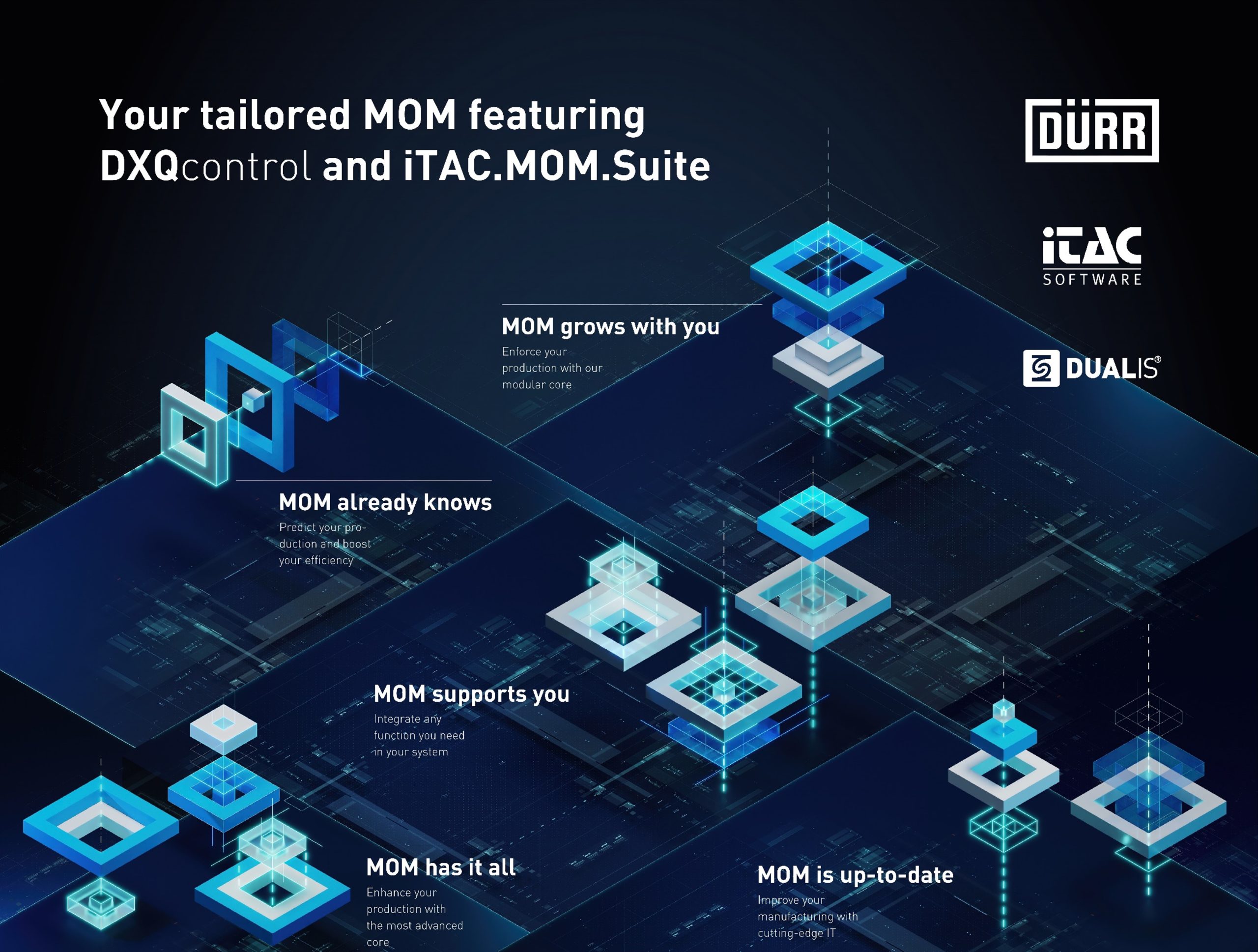
HOW THE INNOVATION WAS INVENTED
Dürr Systems AG and iTAC Software AG joined forces and develop a modular, integrated yet open system. The Manufacturing Operations Management (MOM) bundles all functional areas of the digital factory. Hereby, the Digital Factory uses its manufacturing and digitalization knowledge to combine hardware and software. The modular solution is designed for manufacturing planning, execution, control, monitoring, optimization, and predictive analysis. Instead of monolithic individual solutions, the new Manufacturing Operations Management (MOM) system relies on microservices that provide functionality as required. The solution enables a high level of flexibility and consistency and offers many interfaces in terms of interoperability. There are three central superordinate control components in every digital factory: MES (Manufacturing Execution System) controls and monitors production, SCADA (Supervisory Control and Data Acquisition) collects and analyzes data, and HMI (Human Machine Interface) visualizes production and process flow. Until now, these components, for example, the MES sub-segment, were mostly designed as stand-alone solutions. The Digital Factory has combined their competencies and merged the functional scopes of MES, SCADA, and HMI into a uniform MOM architecture. This was made possible by combining Dürr’s DXQcontrol product family with iTAC’s iTAC.MOM.Suite. Manufacturing companies, whether manufacturers or suppliers, thus receive a future-proof industrial digitalization solution with interoperable modules that cover all smart factory functionalities. While previous MES solutions are monolithically structured, i.e., a single software product encompasses different functionalities, such as data acquisition or logistics, Dürr and iTAC’s MOM architecture takes a modular approach.
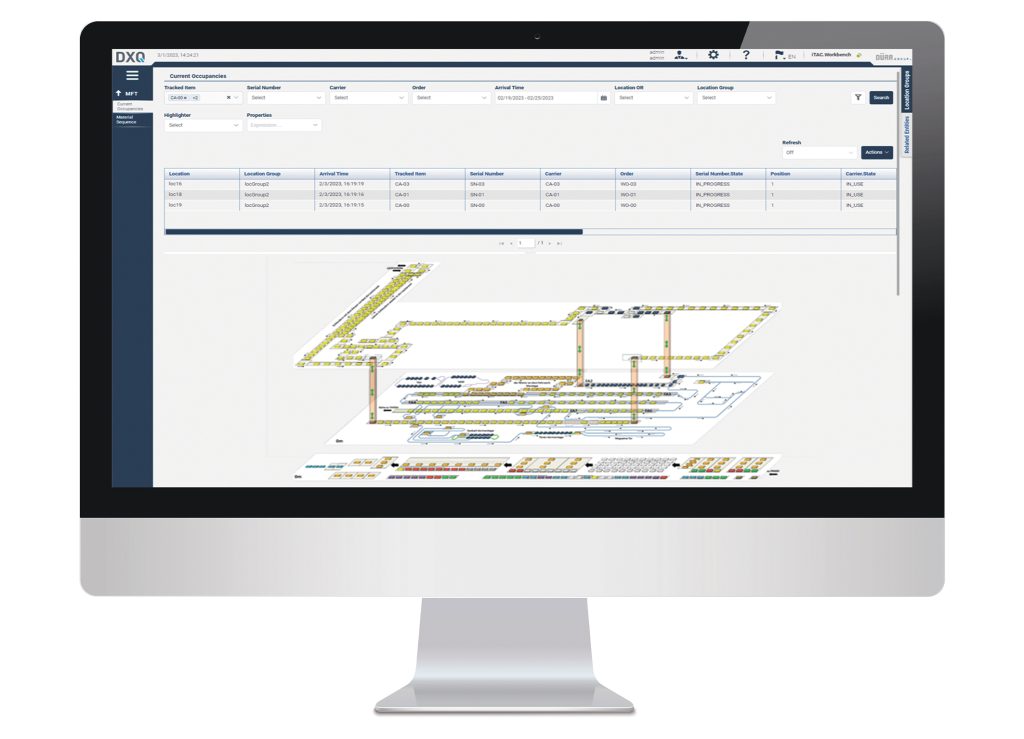
Benefit
- The digital solutions of the Digital Factory combine the software competences with its expertise in production engineering and manufacturing processes. Thanks to Dürr’s and iTAC’s key competences, the Digital Factory is able to strengthen synergies by jointly developing software solutions. Nowadays, the two firms cooperate in one common product development team.
- The latest release of the modular MOM system shows that the Digital Factory stays ahead of technology trends by adopting current software solutions and developing these further. see innovation below.
- A continuous, yet agile software development allows the Digital Factory to keep up with the velocity at which the industry changes.
Contact
Dürr Systems AG Phone: +49 7142 78-3265 Website: www.durr.com
Phone: +49 2602 1065 109 Website: www.itacsoftware.com |
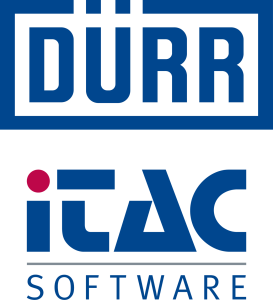